How often should the five-cone water bucket be inspected or maintained? | WM INTERNATIONAL Expert Guide
- How Often Should the Five-Cone Water Bucket Be Inspected or Maintained?
- What Are the Common Issues Detected During Inspections of Five-Cone Water Buckets?
- How Does Maintenance Frequency Impact Water Park Safety and Visitor Experience?
- What Are the Recommended Tools and Techniques for Inspecting Five-Cone Water Buckets?
- Should Maintenance Logs Be Maintained, and What Information Should They Contain?
- When Is It Time to Replace a Five-Cone Water Bucket Instead of Repairing It?
How Often Should the Five-Cone Water Bucket Be Inspected or Maintained?
The five-cone water bucket, a popular interactive water feature in many water parks, requires regular inspection and maintenance to ensure safe and efficient operation. According to ASTM F2476-20, a widely recognized standard for water park attractions, water buckets and tipping bucket systems should be inspected daily for visible signs of wear, corrosion, and mechanical issues. A more detailed maintenance check should be performed monthly, including verifying sensor operation, water flow rates, and structural stability.
Industry best practices recommend comprehensive annual inspections conducted by qualified professionals, including non-destructive testing (NDT) of metal components where applicable. Regular maintenance extends the lifespan of the bucket system and ensures compliance with safety regulations like those from the U.S. Consumer Product Safety Commission (CPSC) and international norms.
What Are the Common Issues Detected During Inspections of Five-Cone Water Buckets?
Common issues include corrosion on metal arms, worn bearings on pivot points, clogged water jets affecting fill rates, sensor malfunctions, and loose bolts or structural components. Early detection of these problems during daily or monthly checks is crucial to avoid operational downtime or safety hazards.
How Does Maintenance Frequency Impact Water Park Safety and Visitor Experience?
Regular maintenance prevents mechanical failures that could injure guests or cause unplanned closures. Consistent inspection enables water park operators to identify and resolve issues proactively, maintaining smooth operation, enhancing guest satisfaction, and complying with occupational health and safety standards.
What Are the Recommended Tools and Techniques for Inspecting Five-Cone Water Buckets?
Inspection tools include visual inspection devices, ultrasonic thickness gauges for metal parts, torque wrenches for tightness testing, and electronic testers for sensors and control systems. Cleaning nozzles and replacing worn seals should be part of routine maintenance to prevent leaks and ensure proper water flow.
Should Maintenance Logs Be Maintained, and What Information Should They Contain?
Yes, maintaining detailed logs is essential. Logs should record inspection dates, findings, corrective actions taken, part replacements, and personnel responsible. This documentation helps track maintenance history, supports regulatory compliance, and assists in warranty claims or audits.
When Is It Time to Replace a Five-Cone Water Bucket Instead of Repairing It?
Replacement is recommended when corrosion or structural damage compromises safety, repair costs exceed 50% of replacement costs, or if the manufacturer has declared the model obsolete with unavailable parts. Upgrading to newer models can also improve water efficiency and reduce maintenance frequency.
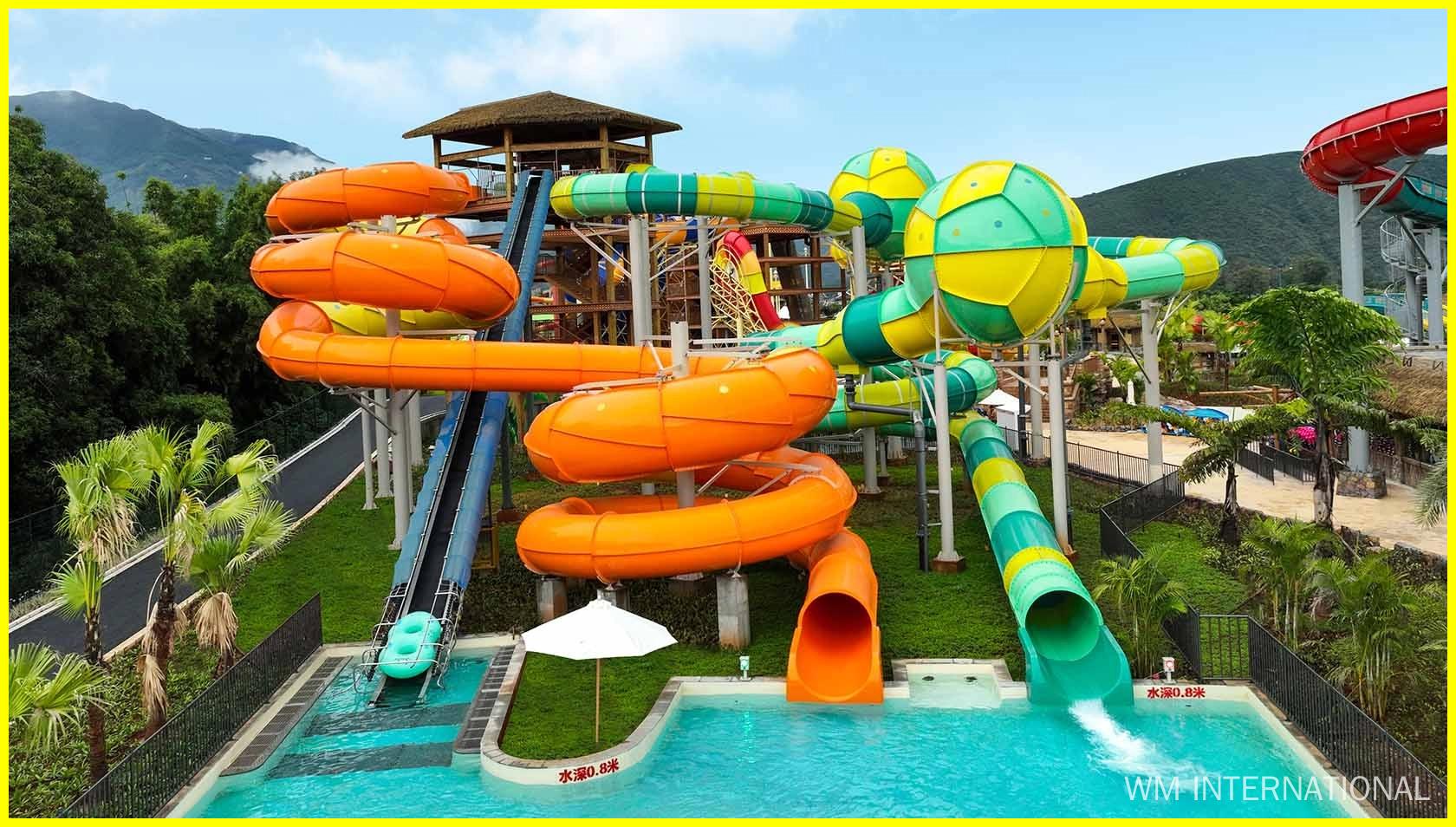
What Material Are Water Slides Made From? Ultimate Guide in 2025
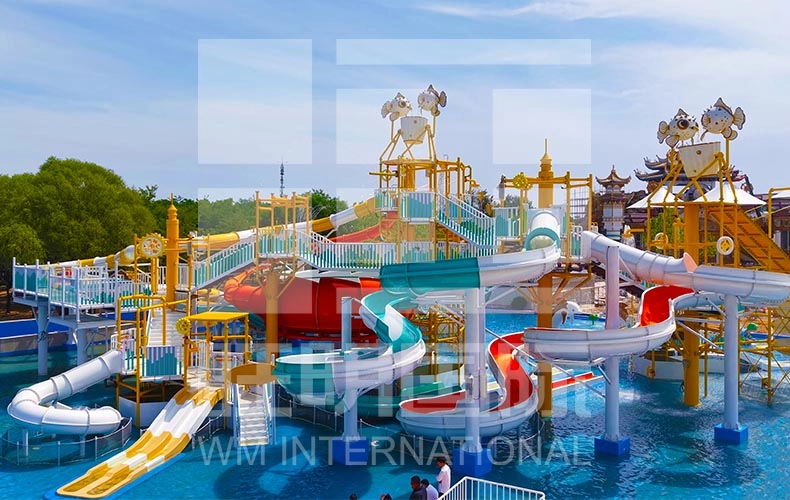
How to Upgrade and Renovate a Water Park
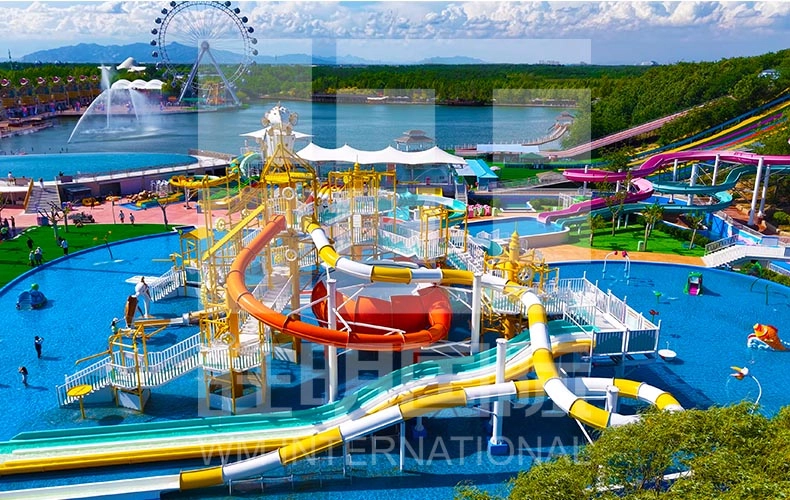
How to Consider Facility Durability When Building a Water Park
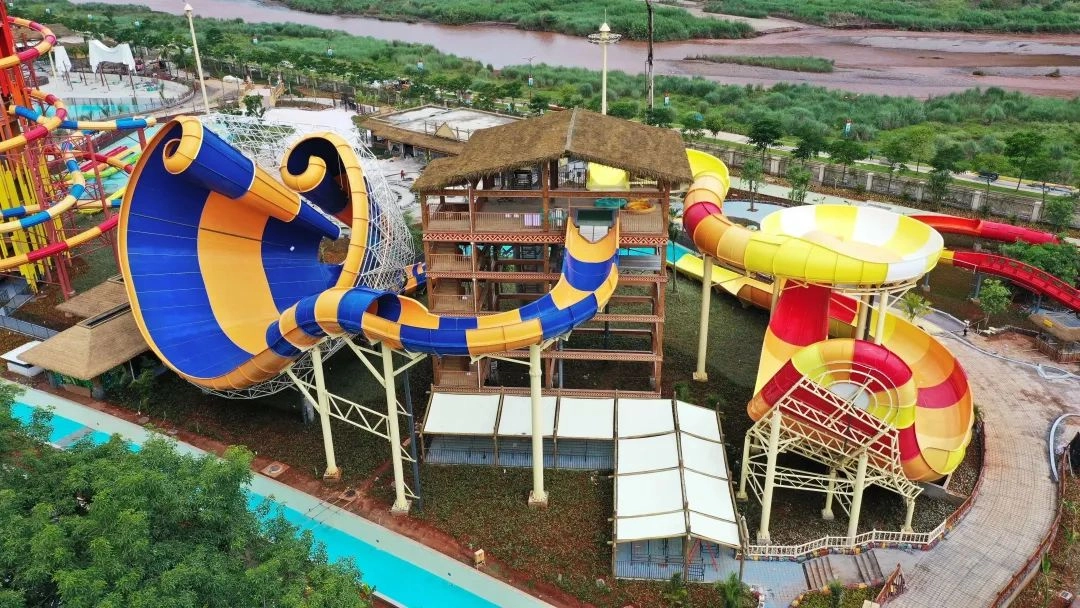
Integrated Resort + Water Park Construction: A Systematic Development Guide
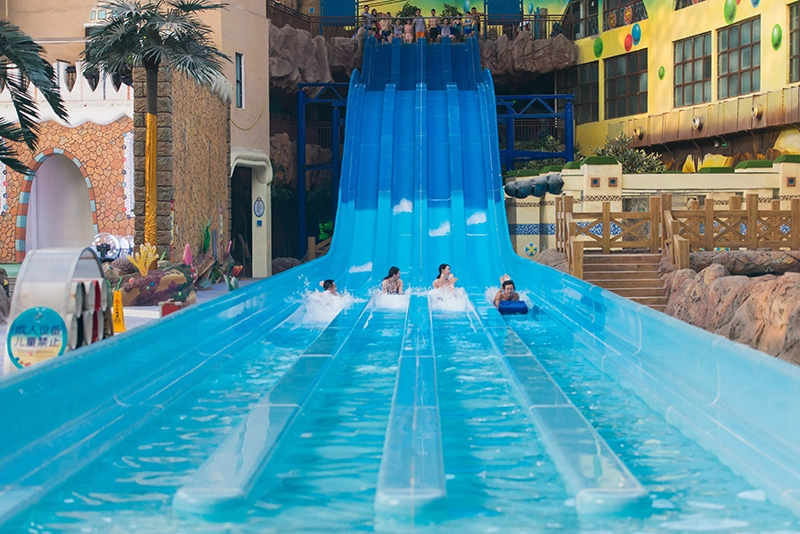
How to Choose a Water Park Equipment Manufacturer
FAQs
What are the advantages of WM International's design team?
Our design team has rich project experience in planning, landscape, architecture, structure, equipment and other fields. The team members include many senior experts at home and abroad to ensure that each project can combine the latest technology and design concepts in the industry to provide the best solutions.
How long does it usually take for WM International's water park design projects to be completed?
The project cycle varies depending on the project size, design complexity and customer needs. Generally speaking, the complete planning and design process usually takes 2-6 months. We will confirm the schedule with the customer at the beginning of the project and ensure that the design work is completed on time.
What are the main contents of water park planning and design services?
We provide a full range of water park planning and design services, including site analysis, theme setting, facility layout, visitor flow design, safety and environmental protection design, etc. Our goal is to create a safe and entertaining water park through scientific planning and creative design to enhance the visitor experience.
How to start working with WM International for water park project design?
You can contact us through our official website contact form or call our customer service team directly. We will conduct initial communication based on your needs, arrange project surveys and analysis, develop personalized design plans, and provide detailed service processes and quotations.
Does WM International provide post-operation and maintenance support for the water park?
Yes, we not only provide design and construction services, but also provide operation and maintenance support for the water park. We can provide equipment maintenance, regular inspections and optimization suggestions according to customer needs to ensure the long-term efficient and safe operation of the park.
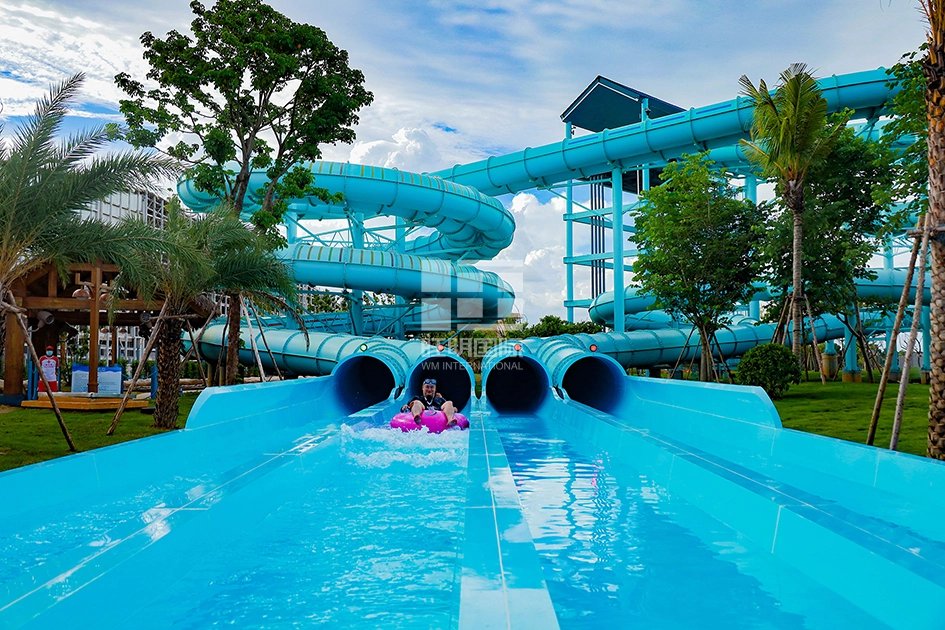
Time Tunnel Water Slide
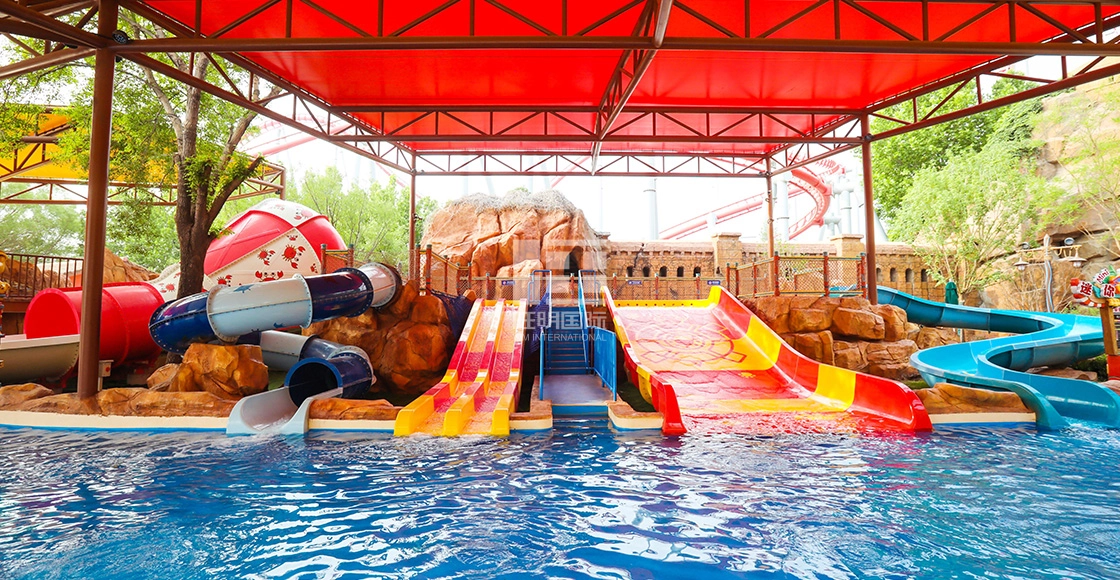
Children Combined Water Slide
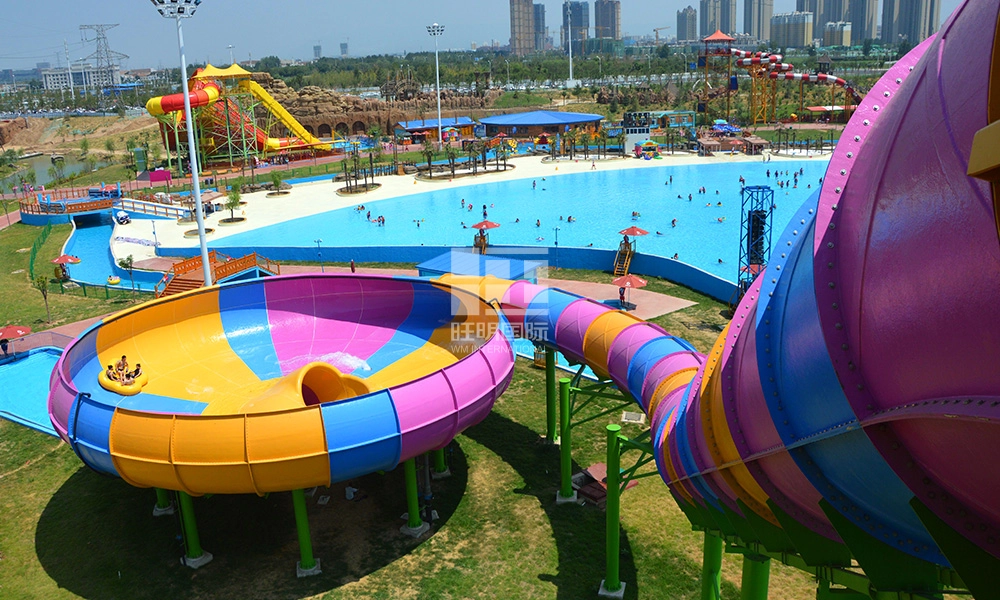
Huge Bowl Water Slide
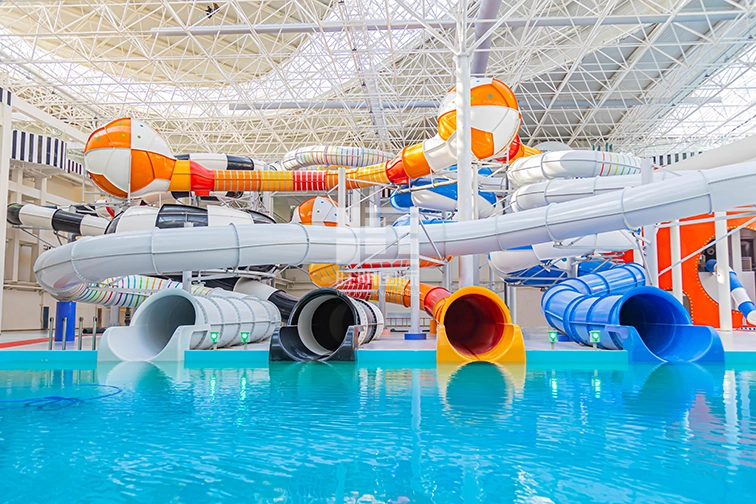
Group Water Slides
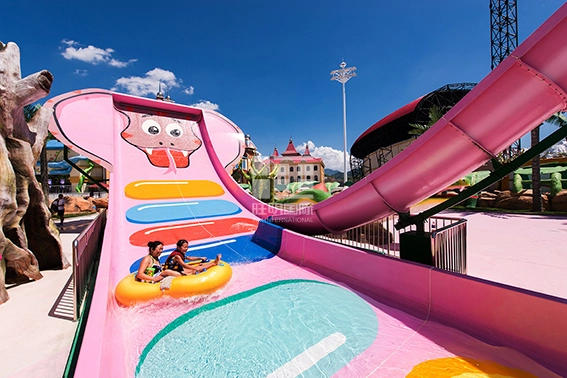
Small King Cobra Water Slide
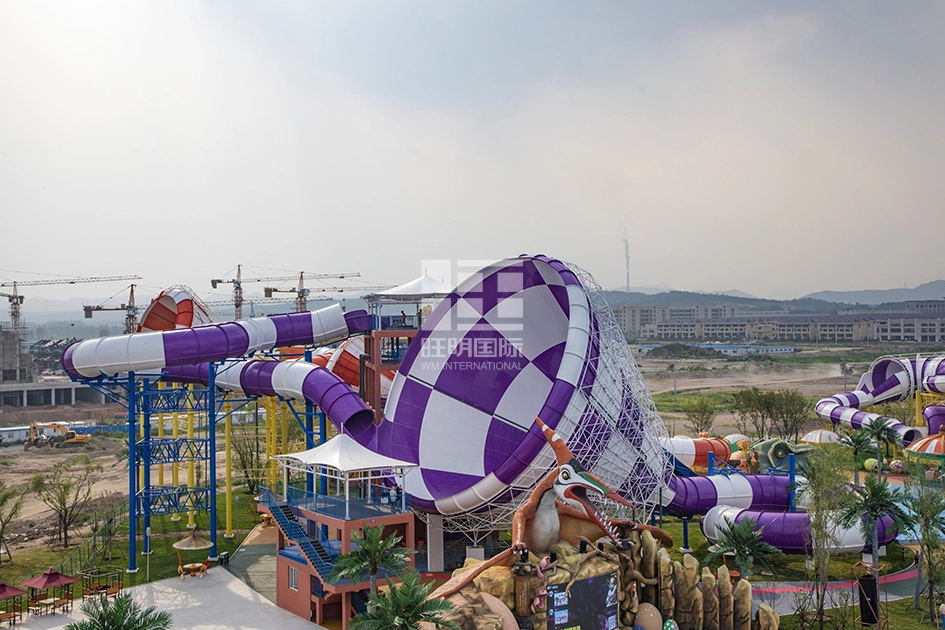
Big Tourbillion Water Slide
Get in touch
Have to get customized water park solutions and product quotes.
We will provide you with professional consultation and support.
wmwaterslide
wmwaterpark